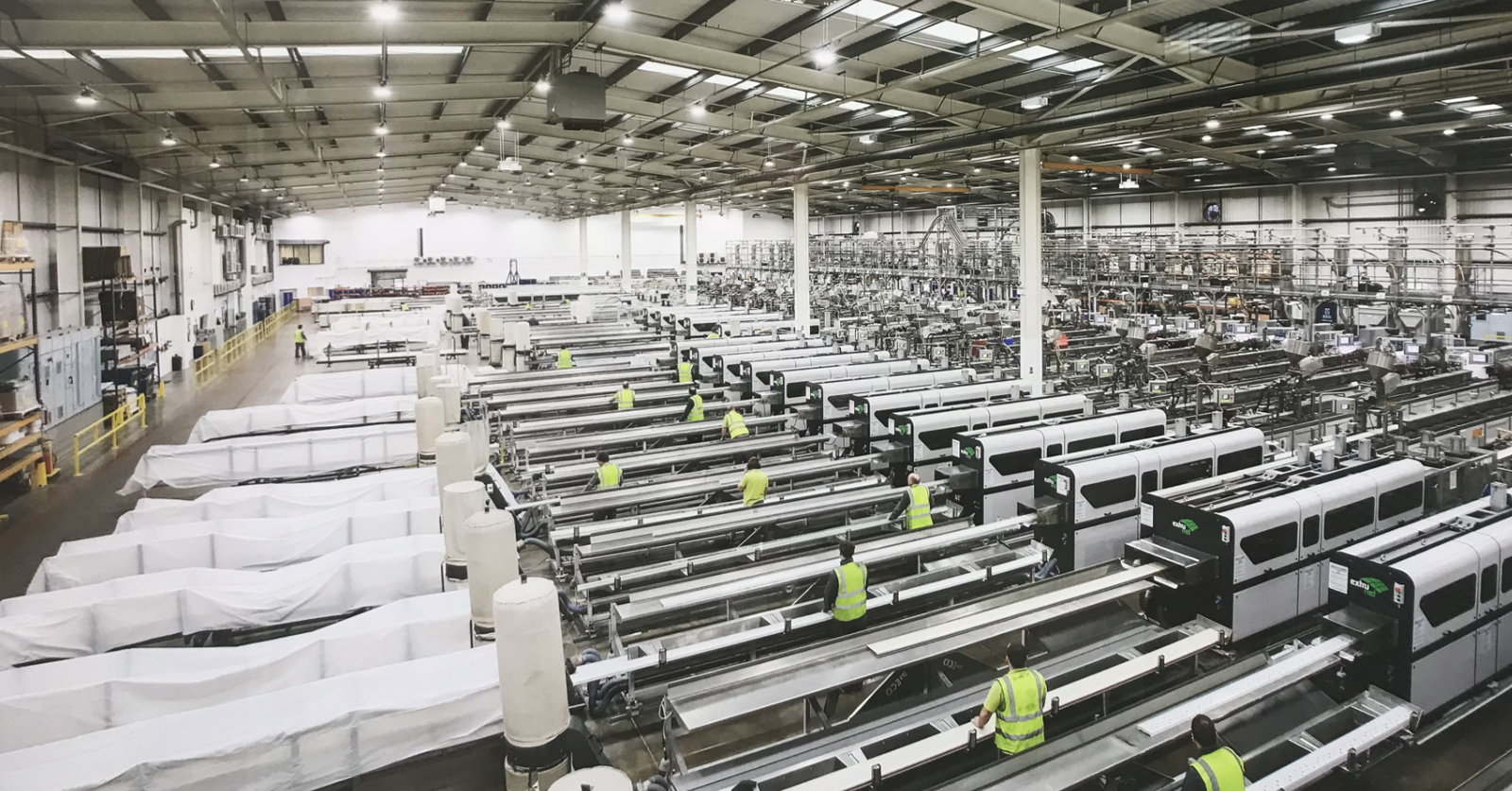
Quanex Building Products Uses Adept Engineering Document Management to Achieve Lean Manufacturing Processes
Company overview:
Quanex Building Products Corporation is an industry-leading manufacturer of components that sells to Original Equipment Manufacturers (OEMs) in the building products industry. Quanex designs and produces energy-efficient vinyl profiles, insulating glass spacers, window and door screens, fenestration components, and kitchen and bath cabinet components.
Goals
- To improve quality and time to market.
- To apply problem solving as a mechanism for change and process improvement.
- To improve engineering processes and steer the company’s adoption of new technology with Lean and Six Sigma methods and strategies.
We’ve always had a problem solving team working with engineering. It started out with drawing standards. Everyone was doing things just a little differently and we wanted to formalize naming and dimensioning conventions and how people stored information. Then it was on to improving our ECO and ECR process. After that, we entered the realm of controlling our data.
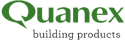
Challenges
- How to manage SolidWorks, Autodesk Inventor, and AutoCAD Lite drawings that make up their models and assemblies for doors, screens and other products.
- They needed to ensure the company passes its ISO certification audits.
- All the company’s disparate systems were in silos and needed to be synchronized into a system that could manage the separate databases and activity without risk of failure or loss of version history.
We were using Windows Explorer to manage all of our CAD files, ECOs, ECRs, ISO documentation—and anything else we could think of.
We had over 6500 different Windows folders where we stored our work. Our CAD documents were being moved in and out of a ‘controlled’ folder, which made it nearly impossible to know which revision we were working on and who else was working on the same file. Documents were getting lost on people’s desks or not being completed on time. We had no way to know if people were accessing the most current version.
Solution
- Adept provides a cost effective solution that is easy to use, maintain and administer. It is able to accommodate multiple sites--since whatever system they chose at one site will eventually be rolled out to their seven other facilities across the country.
- Adept manages all of their separate databases and all their engineering activities.
- Adept ties in with their Lean and Six Sigma process improvement methodologies.
- With Adept the company does more with less people while increasing quality, reducing lead time, decreasing waste of traveling, and eliminating paper.
While training our 43 users, we reviewed everything we’d accomplished to date; created a short to-do list; and focused on best practices for accomplishing our goals.
Results
- Adept manages, tracks and controls all of Quanex’s CAD documents, ECOs, ECRs, Deviations, Quote/Order Acceptance meeting forms, QMS documentation, ISO documentation, and all their Material Safety Data Sheets.
- Adept eliminated all “hand carry” processes.
- Adept streamlined their process of achieving and maintaining ISO certification, a huge competitive advantage for Quanex.
- Quanex has eliminated incorrect documents and wrong revisions in their internal audits.
- The Quality documentation department is now confident that only the latest and the greatest versions are in the system.
- Adept’s workflow helps Quality with their process of formal approvals.
- Adept has delivered measurable increases in engineering’s productivity, with faster improvements and less complexity.
- Adept has become part of the company’s problem solving and their Lean and Six Sigma methodologies to achieve overall business goals.
In the past, we might have had one document in 20 different places in the plant. If there was a change, we’d have to make 20 different copies and distribute them on foot to the shop floor or somebody’s office. It was quite cumbersome. Adept has helped cut down on all our work.